Projects Overview B4/III Failure simulation of structures under impact
B4/III Failure simulation of structures under impact
Motivation
Significant damage can occur to structural elements subjected to impact loads, e.g., object penetration and splinters, which greatly increase the risk of injury to persons inside the structure. To reduce such risks, the performance of the structural elements needs to be understood. This task is challenging for structures made of concrete due to many phenomena, i.e., nonlinear behavior, dis-continuities, and extreme deformations due to penetration and cracking.
State of Research and preliminary work
Taking into account the large deformations of the structures due to impactor penetration, the Material Point Method (MPM) is a suitable numerical approach for discretizing and modelling. The failure of a structure is depicted by the eigenfracture methodology in combination with the MPM (Fig. B4.1). The reinforcing bars are described by finite truss elements within the MPM. In the far-field of the domain, where the deformations are small, the Finite Element Method (FEM) is used. Both methods, MPM and FEM, are coupled to optimize the simulation with respect to accuracy and efficiency (Fig. B4.2).
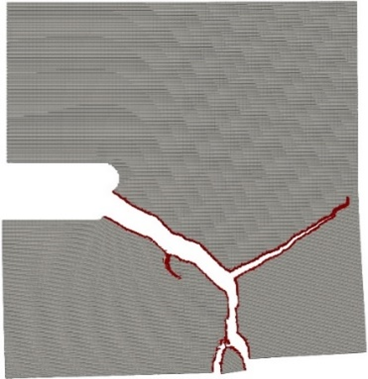
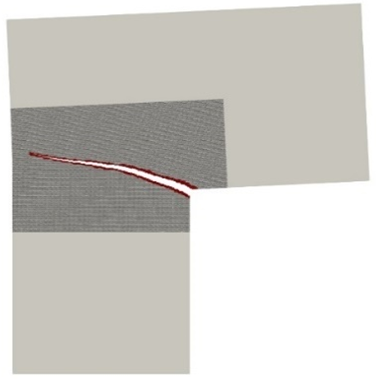
B4.1. Compact tension test simulation by eigenfracture. B4.2. MP-FE method for L-shaped modelling.
Scientific Task and project goals
The coupling between MPM and FEM is planned to be further developed by automated conversion from FEM to MPM of the strongly deformed finite elements during the simulation. The eigenfracture model is to be coupled with the microplane damage model. Additionally, the temperature change during impact loading will be taken into account to determine the material response. As the bending stiffness of the reinforcing bars could have big influence on the structural response, like the dowel-action, the reinforcement is to be described by beam finite elements. The developments and experiences from B4/I and II form a solid basis for the success of B4/III project. The plate and column elements defined as common benchmark examples throughout the RTG 2250 will be core of the structural investigations based on the input of the experimental subprojects.
Interaction with other projects of Cohort III
The collaboration with the numerical projects B1 and B3 leads to reach a realistic description of the material by tuning the material models. The material parameters necessary for the material description are provided by project A3 and A4. The validation of the developed numerical approaches can be achieved by comparing to the experimental test performed in project A5 and the common benchmark examples. Project C1 allows for quantitative validation of the results. Project C3 is pro-vided with all the requested and useful data.
Contributors
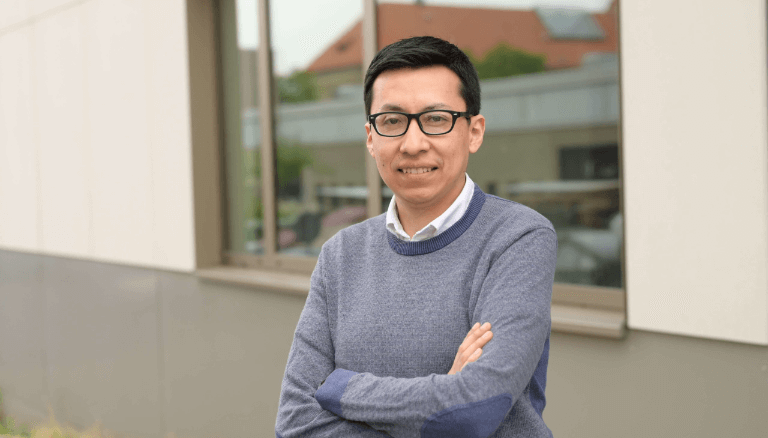
© Dominik Junger
Doctoral Researcher
OSVALDO ANDRES OROPEZA NAVARRO, M.SC.
Institute of Structural Analysis
Technische Universität Dresden
Von-Mises-Bau, 3rd floor, room 201A
Georg-Schumann-Straße 7
01187 Dresden
Germany
- osvaldo_andres.oropeza_navarro@tu-dresden.de
- +49 351 463 32199
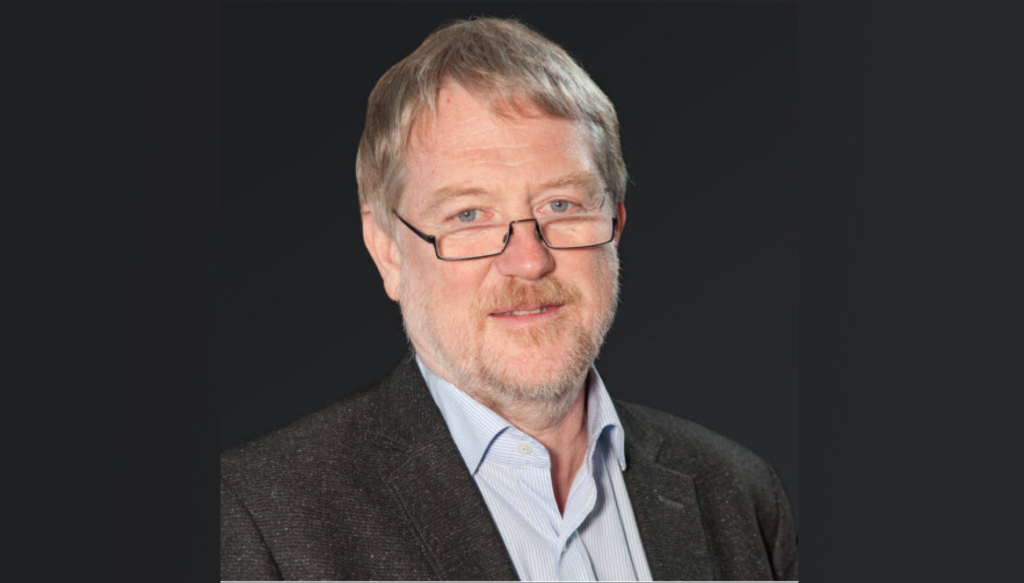
Principal Investigator
Univ.-Prof. Dr.-Ing. habil. Michael Kaliske
Institute of Construction Materials
Von-Mises-Bau (VMB), Room 101A Georg-Schumann-Straße 7
01187 Dresden
Germany
- michael.kaliske@tu-dresden.de
- Institute
- +49 351 463 34386
- +49 351 463 37086
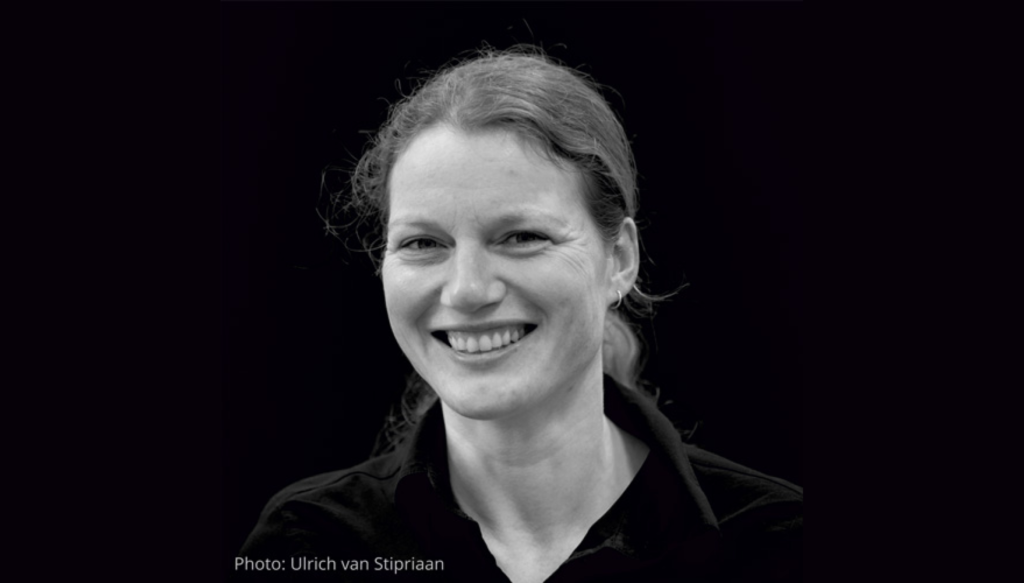
in cooperation with
apl. Prof. Birgit Beckmann
Institute of concrete structures
ABS, Floor 05, Room 027
August-Bebel-Straße 30/30A
01219 Dresden
Germany
- Birgit.Beckmann@tu-dresden.de
- Institute
- +49 351 463 38687
- +49 351 463 37289