Projects Overview A4/III Fully automated reinforcement with mineral-bonded fibre composites
A4/III Fully automated reinforcement with mineral-bonded fibre composites
Motivation
Low productivity and shortage of skilled labour constitute the major challenges faced by construction industry [1]. Therefore, new solutions for retrofitting existing structures towards their high impact resistance imply the use of highly automated, customized processes for producing / applying strengthening layers. While short fibres can be relatively easily integrated into robotized spaying or extrusion-based material deposition processes, the automated integration of continuous yarns or textiles is a challenge still to be mastered. The vision is fully digitized, robotic strengthening technology using a combination of mineral-impregnated carbon yarns and short fibres being part of mineral-based matrix. The approach of using mineral impregnation of yarns seems to be most promising specifically with respect to high technological flexibility it offers.
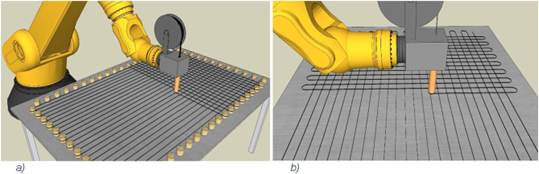
Automated, customized strengthening with mineral-impregnated yarns, adapted from Mechtcherine et al. [2]
State of research and own preliminary work
Previous research at IfB has demonstrated a very high potential of novel digital production technologies. 3D concrete printing based on layered extrusion could be performed in various manner, also using SHCC (Strain-hardening cement-based composites) [3,4]. This technology can be adapted to printing thin strengthening layers on vertical or inclined substrates (the structural element to be strengthened). Application of SHCC by spaying has been demonstrated as well [5], and this process can be robotized. The major reference is, however, the original approach of impregnating carbon yarns with mineral binders and integrating such yarns in further technological processes [2]. Among others, the integration of impregnated yarns in 3D concrete printed has been realized by either inducing the yarn into concrete filament before its deposition or placing yarns between subsequent filaments or even placing yarns independent of concrete deposition [6]. Such approaches can be extended to application for impregnated carbon yarns and mineral matrix on various substrates for purpose of strengthening.
Scientific problem and project goals
- Further developing the inline yarn impregnation with finely dispersed mineral binder suspensions made of sustainable constituents
- Creating the scientific basis for the robotic application of reinforcement layers consisting of mineral-impregnated yarns and cement-based (optionally, short fibre reinforced) matrices incl. matrix flow control
- Characterising the mechanical performance of the novel reinforcement layers under impact loading incl. studying micromechanical parameters of the composites in relation to the production process
- Model description of the rate-dependent mechanical behaviour of new composites
- Developing a robust test method to characterise the bond between reinforcing layers and concrete substrates and investigating of the influence of composition, application technique (especially shotcrete and extrusion), and substrate preparation on the bond properties.
Interaction with other Projects of Cohort III
Possible interactions are envisioned with project A1, in the design and handling of hybrid mineral-impregnated yarns possibly also enabling smart properties. Tests on full-scale strengthened concrete members should be carried out in collaboration with project A5 and A6 to assess the structural performance of strengthening layers on RC beams, columns, and slabs. Furthermore, design considerations should be put forward by modelling the novel composites through mesoscale numerical analyses (project B3), and data-driven approaches (project C3), while a collaboration with C2 is needed with respect to assessing sustainability of the new solutions. This synergistic and multifaceted approach on the topic has the potential of ideally merging into guidelines for practitioners.
References
[1] G. De Schutter, K. Lesage, V. Mechtcherine, V.N. Nerella, G. Habert, I. Agusti-Juan: Vision of 3D printing with concrete – Technical, economic and environmental potentials. Cement and Concrete Research 112 (2018) 25-36
[2] Mechtcherine, V., Michel, A., Liebscher, M., Schneider, K., Großmann, C.: Mineral-impregnated carbon fiber composites as novel reinforcement for concrete construction: Material and automation perspectives. Automation in Construction 110 (2020) 103002
[3] Ogura, H., Nerella, V.N., Mechtcherine, V.: Developing and testing of strain-hardening cement-based composites (SHCC) in the context of 3D-printing. Materials 11 (2018) 1375
[4] Ivaniuk, E., Eichenauer, M.F., Tošić, Z., Müller, S., Lordick, D., Mechtcherine, V.: 3D printing and assembling of frame modules using printable strain hardening cement-based composites (SHCC). Materials & Design 219 (2022) 110757. DOI: 10.1016/j.matdes.2022.110757
[5] Mechtcherine, V.: Novel cement-based composites for the strengthening and repair of concrete structures. Construction and Building Materials 41 (2013) 365-373. DOI: 10.1016/j.conbuildmat.2012.11.117
[6] Mechtcherine, V., Michel, A., Liebscher, M., Schmeier, T.: Extrusion-based additive manufacturing with carbon reinforced concrete: Concept and feasibility study. Materials 13 (2020) 2568.
Contributors
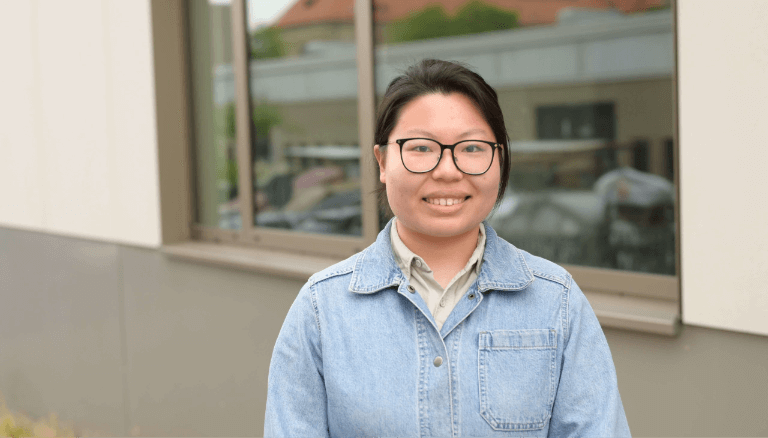
© Dominik Junger
Doctoral Researcher
CHENTAOYA HU, M.SC.
Institute of Construction Materials
Von-Mises-Bau, room 310
Georg-Schumann-Straße 7
01187 Dresden
Germany
- chentaoya.hu@tu-dresden.de
- +49 351 463 42852
- +49 351 463 37268
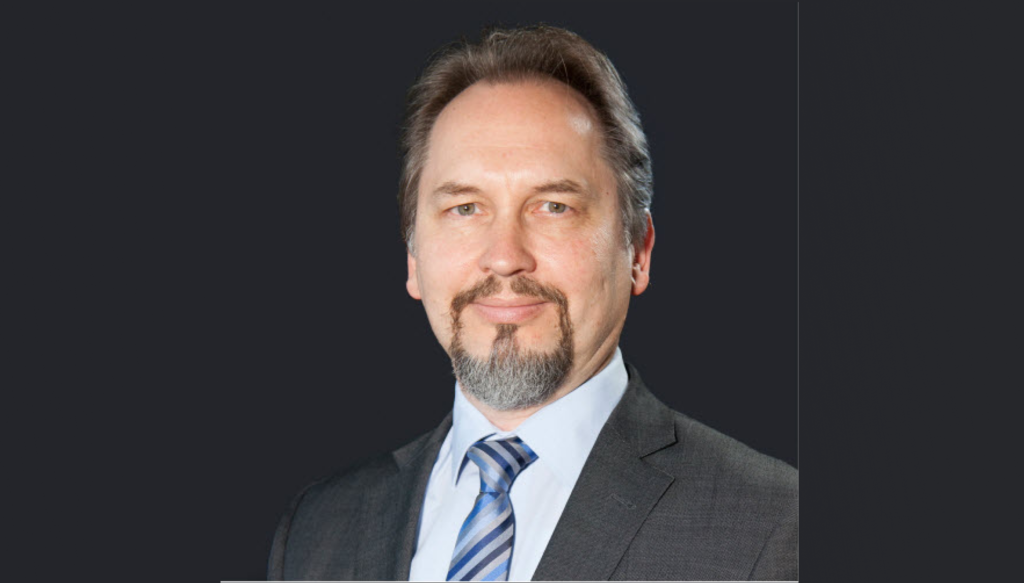
Principal Investigator
Univ.-Prof. Dr.-Ing. Viktor Mechtcherine
Institute of Construction Materials
Von-Mises-Bau, 3rd Floor, Room 315A Georg-Schumann-Straße 7
01187 Dresden
Germany
- Mechtcherine@tu-dresden.de
- Institute
- +49 351 463 36311
- +49 351 463 37268
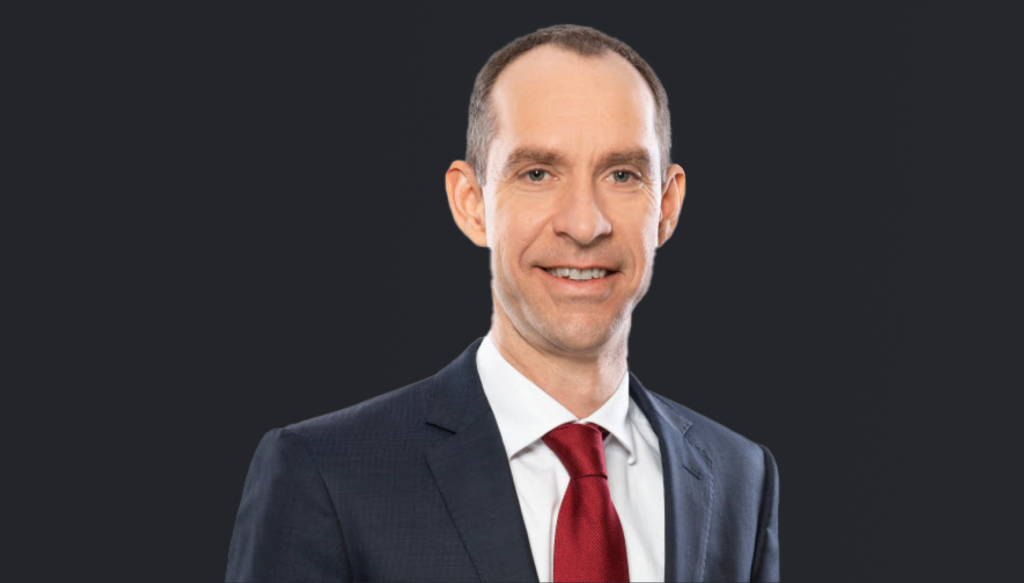
in cooperation with
Prof. Dr.-Ing. Steffen Ihlenfeldt
Institute of Construction Materials
Von-Mises-Bau (VMB), Room 101A Georg-Schumann-Straße 7
01187 Dresden
Germany
- Institute
- +49 (0) 351 463-34358
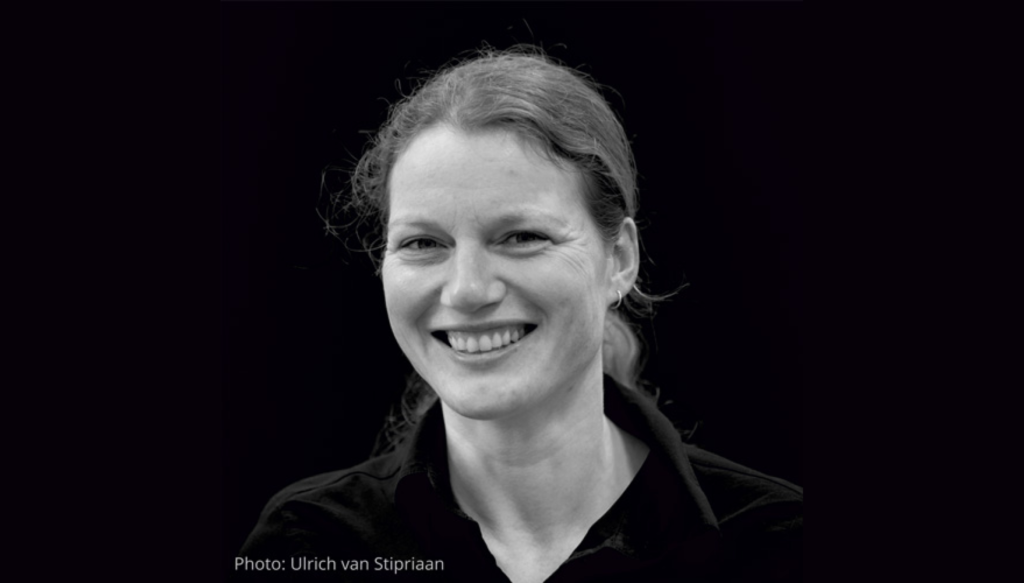
in cooperation with
apl. Prof. Birgit Beckmann
Institute of concrete structures
ABS, Floor 05, Room 027
August-Bebel-Straße 30/30A
01219 Dresden
Germany
- Birgit.Beckmann@tu-dresden.de
- Institute
- +49 351 463 38687
- +49 351 463 37289