Projects Overview A1/II Gradient 3D-reinforcing structures with integrated in-situ sensors
A1/II Gradient 3D-reinforcing structures with integrated in-situ sensors
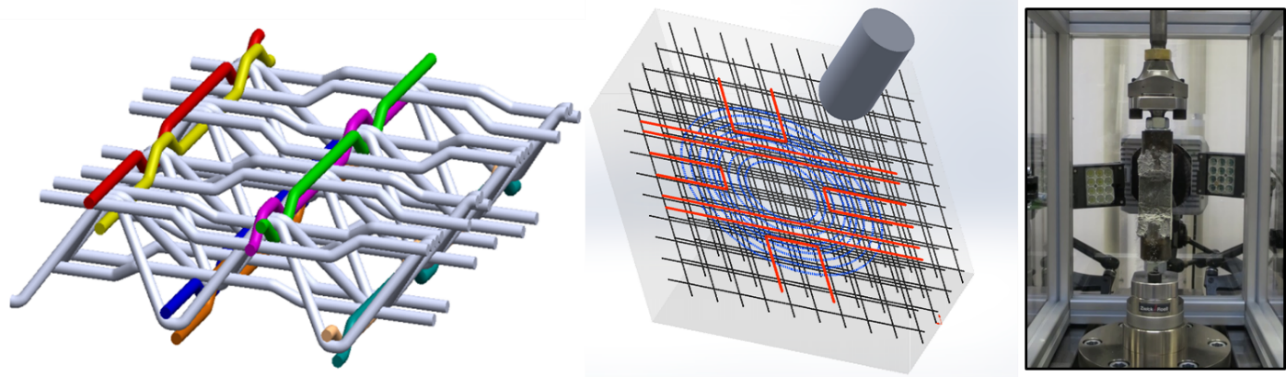
Left to right: Structure and sensor development for reinforcing elements that are based on continuous fibers and suitable for impact scenarios; impact testing technology
Contributors
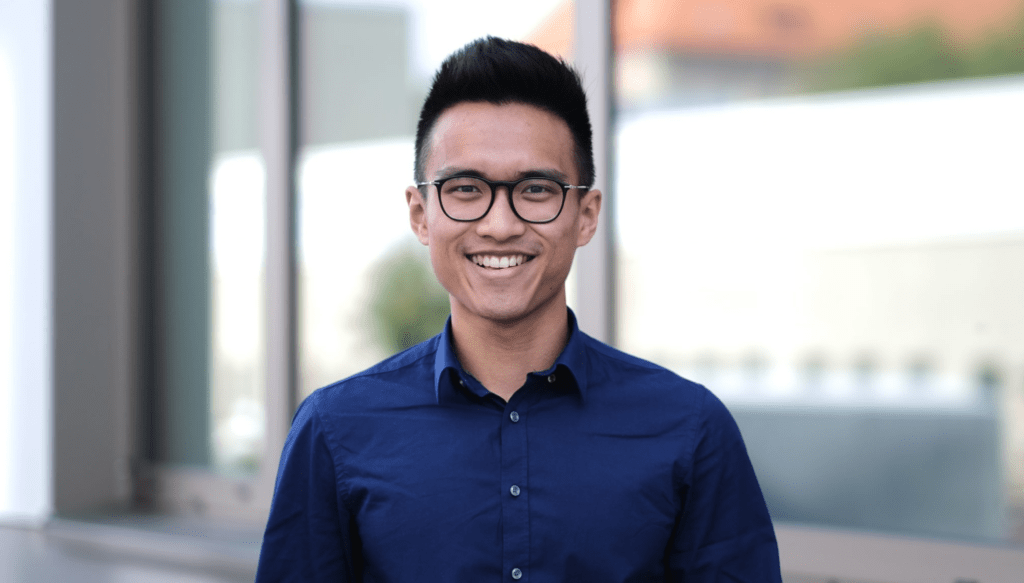
© Tin Trong Dinh
Doctoral Researcher
(2020-2023)
Dipl.-Ing. Hung Le Xuan
Institute of Textile Machinery and High Performance Material Technology (ITM)
at TU Dresden Research group measuring and sensortechnology George-Bähr-Straße 3c
01062 Dresden
Germany
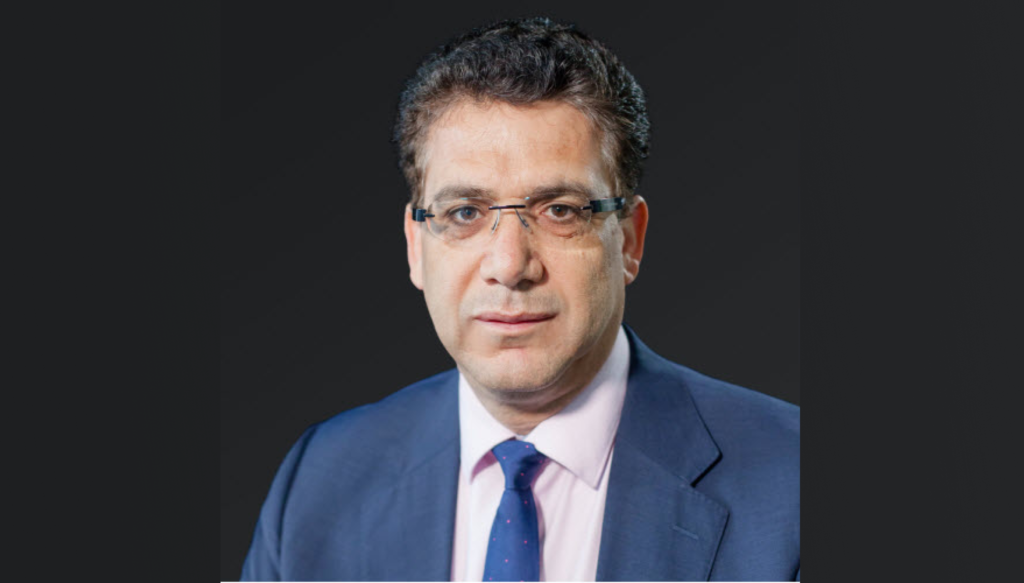
Principal Investigator
Univ.-Prof. Dr.-Ing. habil. Dipl.-Wirt. Ing. Chokri Cherif
Institute of Textile Machinery and High
Performance Material Technology (ITM)
Hohe Straße 6, Room 138
01069 Dresden
Germany
- chokri.cherif@tu-dresden.de
- Institute
- +49 351 463 39300
- +49 351 463 39301
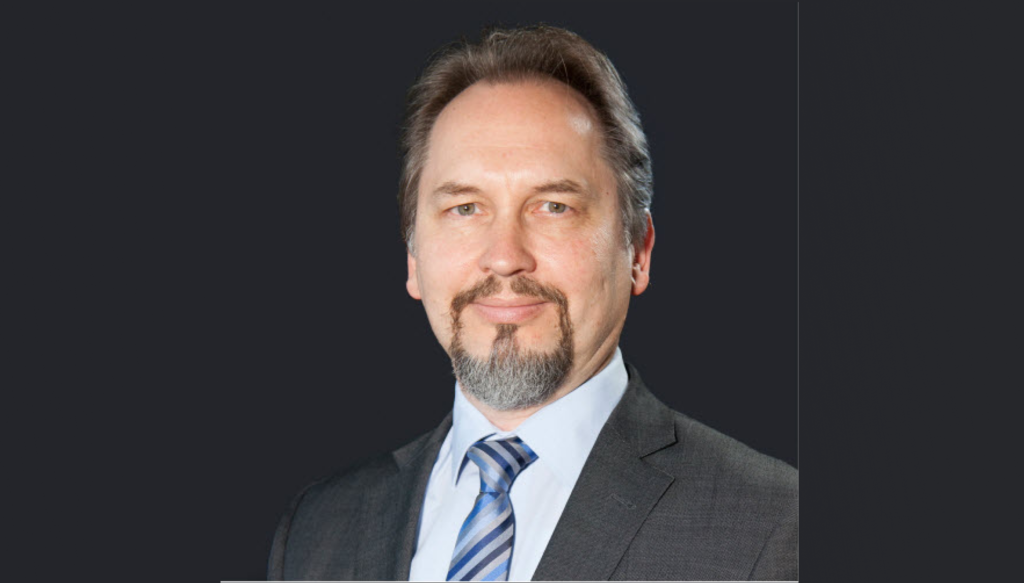
in cooperation with
Univ.-Prof. Dr.-Ing. Viktor Mechtcherine
Institute of Construction Materials
Von-Mises-Bau, 3rd Floor, Room 315A Georg-Schumann-Straße 7
01187 Dresden
Germany
- Mechtcherine@tu-dresden.de
- Institute
- +49 351 463 36311
- +49 351 463 37268
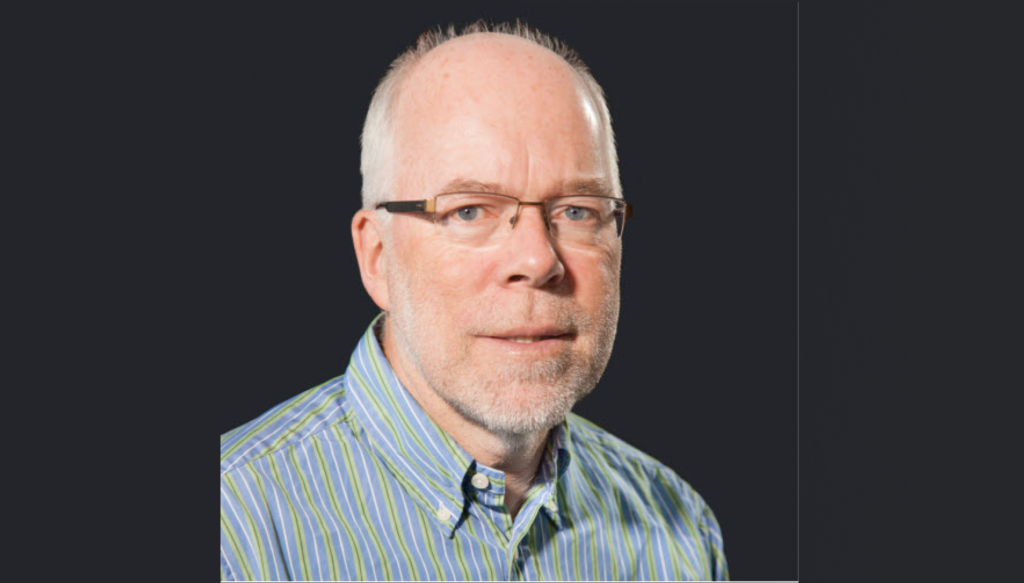
in cooperation with
Prof. Dr. habil. Hans-Gerd Maas
Institute for Photogrammetry and Remote Sensing
Helmholtzstraße 10
01069 Dresden
Germany
- hans-gerd.maas@tu-dresden.de
- Institute
- +49 351 463 32859
- +49 351 463 37266